3D Printed Prosthetic with SMA
Individual Project
Project Mentor: Dr. Bilal Mansoor, TAMU
Spring 2014 - Fall 2014
This project sprung purely out of my curiosity. Wanting to learn more about additive manufacturing and shape memory alloys, I designed and printed a prosthetic arm that incorporated both.
Motivation
After completing my course in Material Science (MEEN 222), I approached the instructor for that course, Dr. Bilal Mansoor, in Spring 2014. I had recently come across Shape Memory Alloys [SMA] (even though they've been around for quite some time...) and wanted to ask him about their structure, and how they managed to retain a memory of their shape.
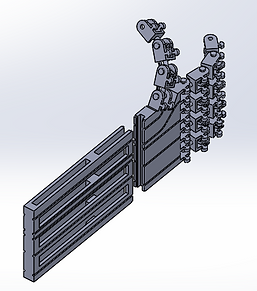
Item 6a: Isometric view of the complete arm
After a long discussion, the professor suggested that I come up with a project that incorporates SMAs and that he'd be willing to cover the costs of the materials from his operating funds. Needless to say, I jumped on the opportunity, and proposed a prosthetic arm, combining the other aspect that I wanted to learn about - 3D printing.
The Project
First, what are Shape Memory Alloys?
Simply put, they are materials (commonly containing Ni-Ti metals) that are malleable at room temperature, but return to their 'memory' state when heated. Say, you take a square sheet of this material and fold it halfway to a rectangle. The square is its original or 'memory' state and if you heat up the folded sheet (by direct heating, or passing an electric current through), the sheet will return to its square form. Heating and deforming beyond the material's "Transition temperature", will change the shape of the material permanently and this new shape will be stored in its 'memory'.
In my project, I tried to utilize this memory effect to actuate the fingers of a 3D printed prosthetic arm. Commercially available Nitinol wires were 'trained' to contract on heating and were surprisingly robust, designed for thousands of cycles heating & cooling under normal operating voltages. They were also rated to exert about 10 N of force during contraction (think: being able to lift a kilogram with just one finger), so they were perfect for my project.

Item 6b: Overall Dimensions. All values in mm.

Item 6c: Close-up of the palm and fingers. The groves are pathways for the SMA wires.
The arm itself was 3D printed and designed on SolidWorks. All the fingers were identical, with the thumb finger set relatively inside the palm, to make it look shorter. Groves were provided in the palm for the Nitinol wires. As can be seen in Item 6d on the right, within the finger, the three digits are dynamically connected via cross links so that a smooth motion is maintained. Below, the video towards the left shows the model in SolidWorks and how, by moving just one digit, the entire finger moves due to the cross links in my design. Also, the video on the right shows a preliminary prototype of the arm, where the finger contracts when I complete the electric circuit due to the shape memory alloy. (The Nitinol wires are too thin to be seen in the video.)

Item 6d: Exploded view of the thumb and fingers. Each finger has 3 digits and 2 cross-links.
While the video on the right shows using a proof of concept, that shape memory wires can replace traditional linear actuators. But a couple of things can be noticed that require further improvement in my design. You will have noticed the rubber band that I had put on the back of the finger. This was to force the finger back to its relaxed stage once the circuit was opened again. A improvement in this direction would be to have two SMA wires for each finger, one on either side to contract and relax the fingers.
Another area of improvement is the actuation time. There is a significant delay between the closing of the circuit and the contraction of the finger. This delay can be reduced by implementing a good feedback controller, using temperature measurements of the SMA wires. While I had not yet taken the controls course by sophomor year and couldn't implement it then, it is one of the things on my to-do list now.