Pneumatic Robot Arm
Individual Project
Project Mentor: Mr. Yasser Al-Hamidi, TAMU
Fall 2012 - Spring 2013
As a freshman, I was hired by Mr. Yasser Al-Hamidi (Mechanical Engineering dept. laboratories' manager), to work on a Mitsubishi industrial robotic arm. I created a demonstration that secured me the First place in the annual Visualization Competition and a professional development grant.
Background
The focus of the project was on a pneumatically operated Mitsubishi RV-2sDB arm. This robot was a part of a larger 'mock production line' setup inside the Controls & Automation Lab at Texas A&M-Qatar. The arm had 6 axes of rotation and could be programmed using Melfa Basic language. At that time, the arm was not being actively used in any coursework at the university, since it had only recently been acquired. My task was to study the robot's potential for use in mechanical engineering coursework.

Item 9a: Representative image of the Mitsubishi RV-2sDB arm. Taken from the web.
The Project
I spent the first few weeks in the project learning to use the Melfa programming language and the operation of the robotic arm. Then, using the CIROS Robotics studio software that was provided with the system, I modeled the entire production line in the laboratory, even though I was only working on one of the components (the robotic arm). This was to help any future projects working on the system, with a ready-made 3D model. A comparison of the model I assembled and the real system at the lab is provided below.
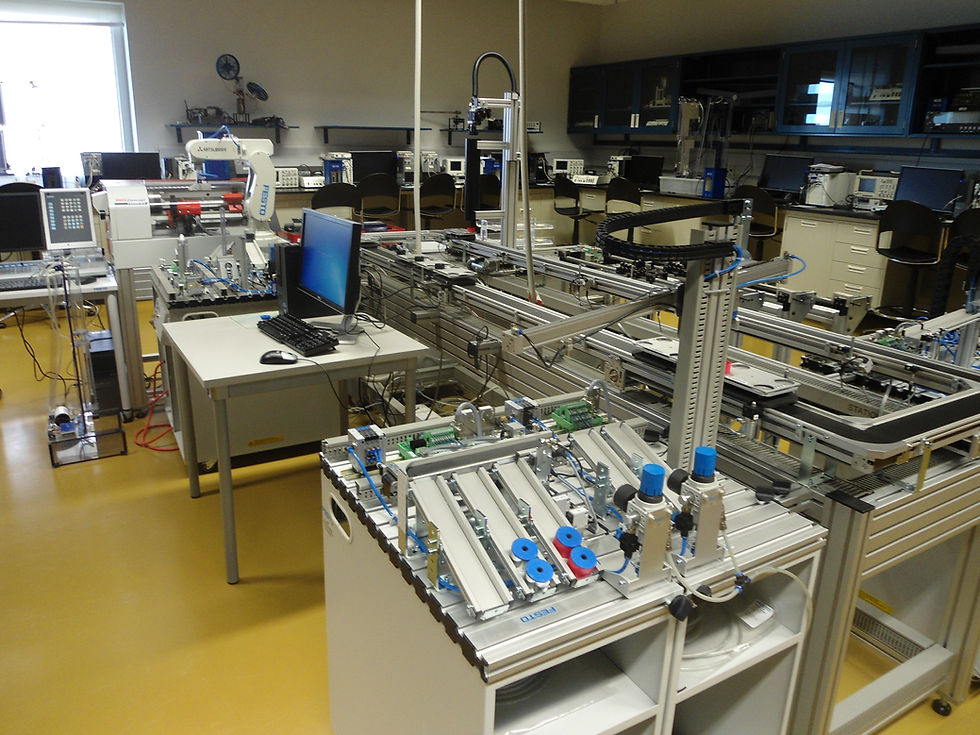
This is (a more cluttered version of) the complete system at the Controls & Automation lab. The robotic arm is towards the left rear.

This is the 3D model that was assembled using CIROS Robotic Studio. Some of the industrial equipment had 3D geometries that I could import, while I had to assemble other components within the software
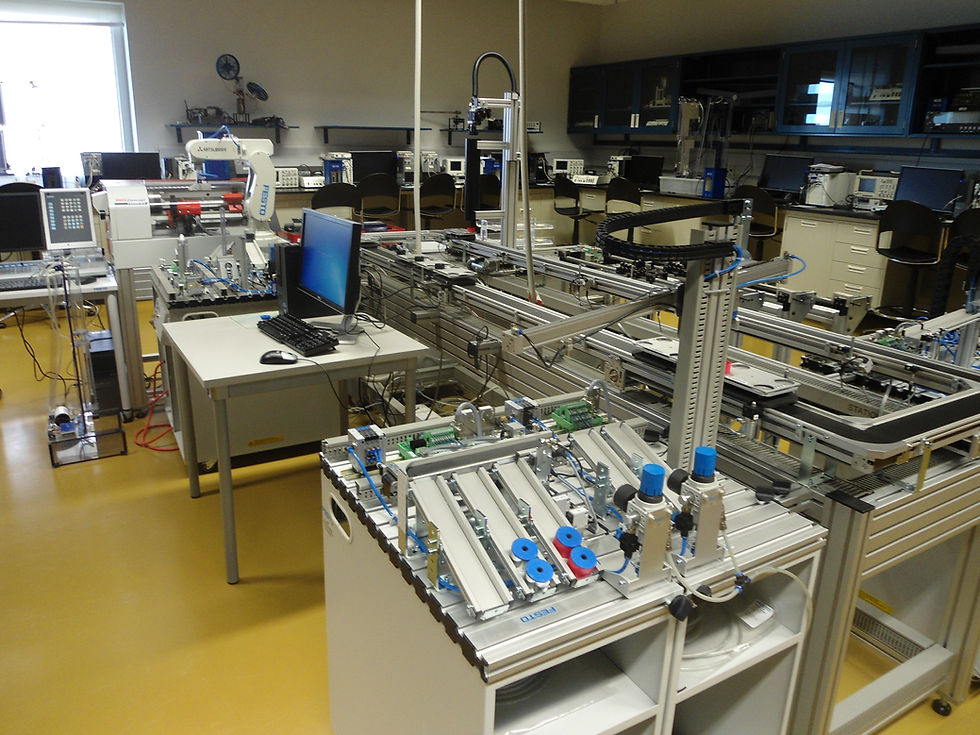
This is (a more cluttered version of) the complete system at the Controls & Automation lab. The robotic arm is towards the left rear.
The Competition
The Visualization Development Competition is held annually by the Research Computing group at Texas A&M University at Qatar, to recognize innovative uses of 3D projection technology.
After successfully modeling the system in CIROS and programming the robot, I created a short demonstration to be presented at the 3D CAVE ( Cave Automatic Virtual Environment) facility at the university. My presentation showed how projects around collision detection and path planning, which use the robotic arm, could be incorporated into Mechanical engineering curriculum, through a synergy between a 3D simulation and programming the real system.
Below is a snip of the simulation video extracted from the CIROS software. There are two streams (Think of them as one for the right eye and one for the left) to be fed to the 3D projectors of the immersive visualization facility.
Apologies for the choppy video. I had to significantly down-sample and reduce the resolution, since the full video was about 8 GB.
Video doesn't load? Click here